Corrugated board is one of the important factors in the production of corrugated board. The poor flatness of corrugated board paper will result in various arch shapes of corrugated board, easy to get stuck during mechanized adsorption printing and cause the paper board to be scrapped and forced to be shut down for cleaning; uneven inking, inaccurate color matching, and gaps in color overlapping edge are easy to occur in two-color printing or multi-color printing; the size displacement of the upper and lower groove on the printing machine will cause overlapping or non seam of the upper and lower covers of the carton; die cutting and feeding will also be produced The defects such as sticking and size displacement may lead to the secondary waste of positive paperboard, or equipment damage, and forced to stop finishing. In a word, the poor flatness of paperboard will make feeding inconvenient and lead to the increase of secondary waste products in the production process.
In order to improve the flatness of corrugated material class, ensure the qualified rate of product quality and normal production efficiency, we have been testing and analyzing constantly in the production practice of cartons, and found out some improvement methods. It is summarized as follows for reference only.
The appearance of corrugated board with poor flatness can be divided into three types: transverse arch, longitudinal arch and arbitrary arch.
Transverse arch refers to the arch formed along the corrugated direction. Longitudinal arch refers to the arch produced by paperboard along the speed direction of the production line. An arbitrary arch is an arch that fluctuates along any direction. The arch on the surface of the paper is called positive arch, that on the surface of inner paper is called negative arch, and that on the surface of inner paper has ups and downs is called positive and negative arch.
Main factors affecting the flatness of paperboard
1. There are different kinds and grades of paper inside. There are imported and domestic kraft paper, imitation kraft paper, corrugated paper, tea board paper, high-strength corrugated paper, and so on, and is divided into a, B, C, D, e, grade. According to the difference of paper materials, the surface paper is better than the inside paper.
2. The main technical parameters of inner paper are different. In view of the performance requirements of cartons or the cost reduction considerations of users, the paper inside the cartons is required to be different
(1) The amount of paper inside is different. Some of the top papers are bigger than the inner ones, and some are small ones.
(2) The moisture content of the paper in the face paper is different. Due to the different environmental humidity of the supplier, transportation and inventory, the moisture content of the surface paper is higher than that of the inner paper, and there are also some small ones.
(3) The paper weight and moisture content are different. First, the surface paper is larger than the inner paper, and the moisture content is greater than or less than that of the inner paper. Second, the surface paper weight is less than the inner paper, the moisture content is greater than the inner paper or less than the inner paper.
3. The moisture content of the same batch of paper is different. The moisture content of one part of paper is higher than that of another part of paper or cylinder paper, and the moisture content of outer edge and inner core side is different.
4. The length of heating surface (wrap angle) of paper passing through heat exchanger is not properly selected and adjusted, or the length of heating surface (wrapping angle) cannot be adjusted arbitrarily. The former due to improper operation, the latter due to equipment limitations, affecting the preheating and drying effect.
5, it is not possible to use steam spray device or equipment without spray device properly, so that humidity of paper can not be increased arbitrarily.
6. The time of moisture emission after preheating is insufficient, or the environmental humidity is large, the ventilation is poor, and the production line speed is improper.
7. Single side corrugating machine, glue machine on the amount of improper, uneven, and the introduction of paperboard shrinkage uneven.
8. Insufficient and unstable steam pressure, steam trap and other accessories damage or pipe water is not drained, resulting in the normal and stable operation of the preheater.
In view of the problem of how to improve the flatness of paperboard, the physical properties, process equipment and other related factors and parameters of several commonly used paper are tested and briefly analyzed.
(1) The same kind of paper quantitative increase, shrinkage slightly reduced. The relationship among the ration, moisture content and shrinkage of some imported kraft paper, domestic kraft paper, tea board paper and high strength corrugated paper was studied.
(2) The steam pressure supplied by corrugated board production line is directly proportional to the surface temperature of preheater. The higher the air pressure. The higher the surface temperature of preheater is.
(3) The paper with large quantity and high moisture content is slow to preheat and dry, otherwise it is fast. The paper with different weight and moisture content is preheated and dried on the air pressure 1.0mpa/cm2 (172 ℃) preheater.
(4) The longer the heating surface length (wrap angle) is, the lower the moisture content is. The relationship between the length of heating surface and moisture content after drying of different weight paper with moisture content of 10% at 172 ℃ and production line speed of 0.83 M / s.
(5) After preheating, the moisture content of single-sided corrugated paper is slow, and the return powder of fan ventilation is fast. The moisture content of 220g / m2 and 150g / m2 single-sided corrugated paper is 13% after being preheated at 172 ℃. In the environment of 20 ℃ and 65% humidity in greenhouse, the speed of natural moisture emission is compared with that of fan ventilation.
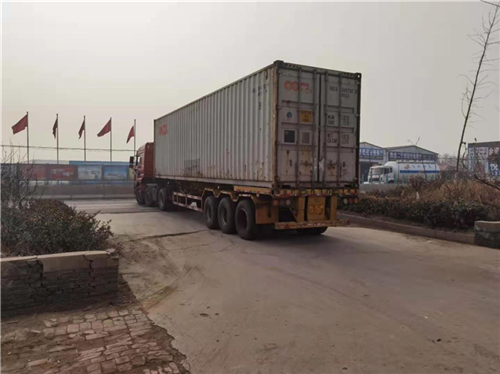
The above test results show that the shrinkage rate of paper is different with different paper weight and moisture content, which is an important physical property of paper. With the same material, the paperboard is easy to achieve good flatness. The opposite is difficult. It is necessary to consider the changes of the above five main factors and make appropriate adjustment. The good or bad flatness depends on the shrinkage rate of each layer of paper. In order to make the paperboard have better flatness, the shrinkage rate of each layer of paper must be basically the same, among which the most important is the inside paper. The shrinkage rate of the front paper is smaller than that of the inner paper, and it is positively arched, otherwise it is negative arch. If the shrinkage rate of the inner paper is uneven, it will become a positive and negative arch. From the analysis of the forming process of the paperboard in the production line, the control of shrinkage can be divided into two stages.
(1) The formation stage of corrugation. That is to say, the process from feeding to secondary gluing is the key stage to control shrinkage. According to the actual situation of the paper, steam pressure, ambient temperature and humidity of each layer of the tile, the parameters of the preheating temperature, the length of the heating surface, including the length of the heating surface, the water distribution of the ventilation, the steam spray, the gluing quantity and the technical parameters of the production line speed lamp are selected respectively, so that all layers of paper can be freely contracted by proper and effective process control, and the final shrinkage rate is basically the same.
(2) Paperboard forming stage. That is, the second gluing to the next process of bonding, drying and ironing. At this time, each layer of paper can no longer shrink freely, and the shrinkage of each layer of paper is restricted by each other after being glued into paperboard. The bonding point can be said to be the starting point of paperboard arch. It is necessary to select and adjust the technical parameters, such as glue amount, drying plate temperature, production line speed, etc., to control the difference of shrinkage rate to the minimum, and iron the arch shape produced by paperboard as far as possible.
First, it is required that the base paper provided by the supplier should have qualified and stable quantitative and moisture content. During transportation and loading and unloading, it is required to keep the basic constant environmental humidity during storage in the factory.
The other is to use the same kind of paper or paper with the same quantity, moisture content and grade as much as possible.
The three is that the length of the heating surface (wrapping angle) of the preheated water heater with large moisture content is increased, the fan is ventilated, the water distribution time is increased, the speed of the production line is slowed down, and the moisture content of the paper is reduced by the length of the heating surface of the preheater, the natural ventilation and steam spray are used to speed up the production line.
Fourth, each layer of paper on the amount of glue to keep consistent, along the corrugated direction on the full width of uniform and moderate amount.
Fifth, the air pressure is stable, and the drain valve and other pipe fittings maintain normal functions.
There are many factors that affect the flatness of corrugated board. The factors of flatness change with each other. The improvement should be made according to local conditions and targeted, and the main contradiction should be grasped and solved. The following is the common problems in the production of single and double corrugated paperboard in our factory, for example.
It is known that: the top paper is 250G / m2 grade 2A kraft paper with moisture content of 7.7%; tile paper is 150g / m2 domestic high strength corrugated paper with moisture content of 10%; inner paper is 250G / m2 grade 2B kraft paper with moisture content of 14%; air pressure of 1.1mpa/cm2 production line speed of 60m / min. Improvement method:
(1) The length of lining (clip) paper passing through the heating surface of preheater (wrap angle) is increased by 1 to 1.6 times and 0.5 to 1.1 times respectively.
(2) The middle speed ventilation of 0.9Kw electric fan is adopted at the moving position of lining (clip) tile line on the bridge of production line, and the windows of workshop are opened for natural ventilation.
(3) a small amount of steam spray on tissue.
(4) The speed of the production line is reduced to about 50M / min.
According to the above selection parameters, the original transverse arch can disappear.
The paperboard is negatively arched from the longitudinal direction
Improvement method:
(1) In front of the three-layer heater, the movement resistance of the tissue paper is increased, and the rotary braking force of the cylinder paper is increased.
(2) The guide wheel and tension wheel in front of the three-layer heater reduce the motion resistance.
After proper adjustment, the original longitudinal arch can disappear.
It is known that the top paper is 200g / m2 grade 2B imitation kraft paper, the moisture content is 8%, the air pressure is 1.0mpa/cm2, and the production line speed is 50M / min. Improvement method:
(1) The length of surface (sandwich) paper passing through the heating surface of preheater is increased by 0.9 to 1.4 and 0.6 to 1.12 times respectively.
(2) lining paper reduces the length of the heating surface of the preheater or uses a small amount of steam spray.
(3) The speed of the production line increased to about 60m / min.
The paperboard is negative arch in longitudinal direction
Improvement method:
(1) The paper in front of the three-layer preheater reduces the movement resistance and the rotary braking force of the cylinder paper.
(2) The guide wheel and tension wheel of lining paper in front of the three-layer preheater increase the movement resistance. After proper adjustment, the original longitudinal arch can disappear.
It is known that: the top paper is 200g / M2b kraft paper, the moisture content is 13%; the (clip) tile paper is 150g / M2 high strength corrugated paper with moisture content of 10%; the inner paper is made of 200g / M2b grade imitation kraft paper with moisture content of 8%; the air pressure is 1.0mpa/cm2; the production line speed is 50M / min. Improvement method:
(1) The length of surface (sandwich) paper passing through the heating surface of preheater is increased by 0.9 to 1.4 and 0.6 to 1.1 times respectively.
(2) lining paper reduces the length of the heating surface of the preheater or uses a small amount of steam spray.
(3) The production line speed increased to about 60m / min.
The paperboard is negative arch in longitudinal direction
Improvement method:
(1) The paper in front of the three-layer preheater reduces the movement resistance and the rotary braking force of the cylinder paper.
(2) The leading tension of Liwa line in front of the three-layer preheater increases the movement resistance.
The cardboard is in a positive and negative arch
There are two kinds of positive and negative arches, and the improvement methods are different. Here we only explain the common transverse positive and negative arches.
Post time: Mar-31-2021